MIL-STD-167: Mechanical Vibrations of Shipboard Equipment
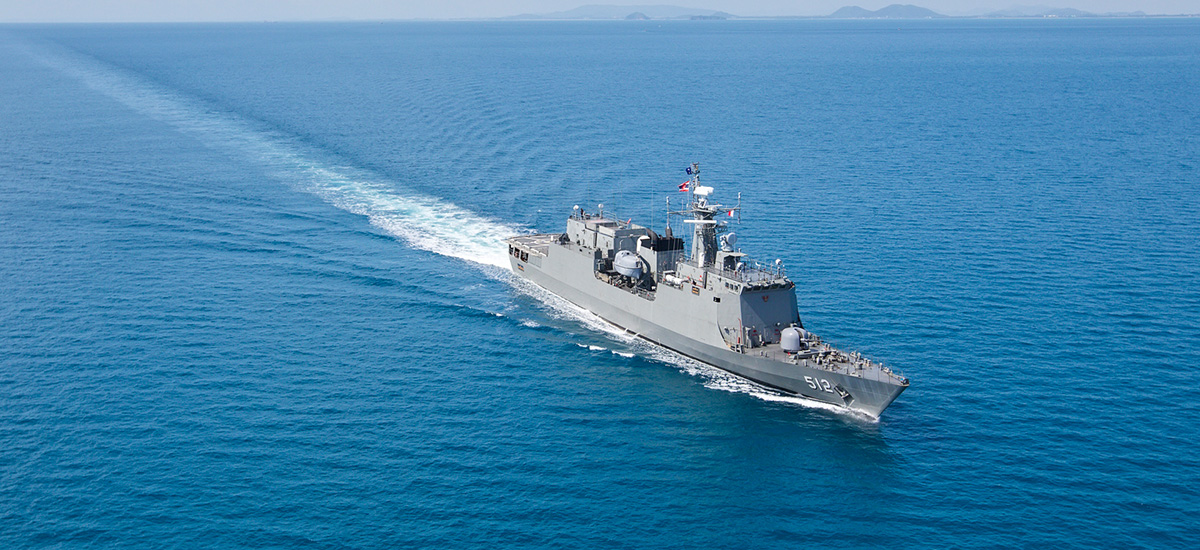
Wherever military vessels go, they are exposed to some form of vibrations on their journey. It is essential to ensure the onboard equipment can remain operational despite these conditions, which is where MIL-STD-167 vibration testing standards come into play.
MIL-STD-167, or the Mechanical Vibrations of Shipboard Equipment, is a military standard the United States Department of Defense (DoD) set out for military equipment reliability testing. It specifies the testing requirements for mechanical vibrations of equipment intended for use on naval ships. This standard is designed to ensure that equipment on these vessels can withstand vibrations from typical naval operations without suffering damage or performance degradation.
What Is MIL-STD-167?
The MIL-STD-167 standard aims to verify that shipboard equipment can endure certain mechanical vibrations common on naval vessels. This test helps prevent failures that can compromise the equipment’s performance or the safety of the crew onboard during an emergency. A certification confirming compliance with this standard shows that manufacturers’ equipment meets the necessary vibration resistance requirement for use in naval applications. Its importance lies in proving the following equipment capabilities:
- Reliability:Â The tests for this standard prove the equipment’s reliability under the dynamic conditions it may experience at sea.
- Performance:Â The MIL-STD-167 test ensures that equipment performs as it should without degradation due to vibration.
- Durability:Â MIL-STD-167 also verifies that onboard equipment can withstand prolonged exposure to shipboard vibrations over its operational life.
- Safety:Â Testing equipment to ensure it meets these requirements helps to prevent equipment failure that can impact mission success.
History and Evolution
The first version of MIL-STD-167 was part of a broader initiative to develop standardized testing for shipboard equipment. Its initial release offered comprehensive guidelines and specific procedures for testing the mechanical vibrations of shipboard equipment.
Since its first publication in 1974, the outline has undergone several revisions to reflect technological advancements and changes in naval vibration testing standards. Updates like these keep the standard relevant and effective in meeting naval equipment’s evolving challenges. Major updates over the years include:
- The distinction between MIL-STD-167A, Type I and MIL-STD-167B, Type II vibration test types.
- Frequency range and testing parameters that align with changing operational profiles and designs of modern vessels.
- Testing technology advancements, adopting more precise sensors and data acquisition systems.
- MIL-STD-167 is periodically revised to harmonize with other military and international standards to cover various operational and environmental factors.
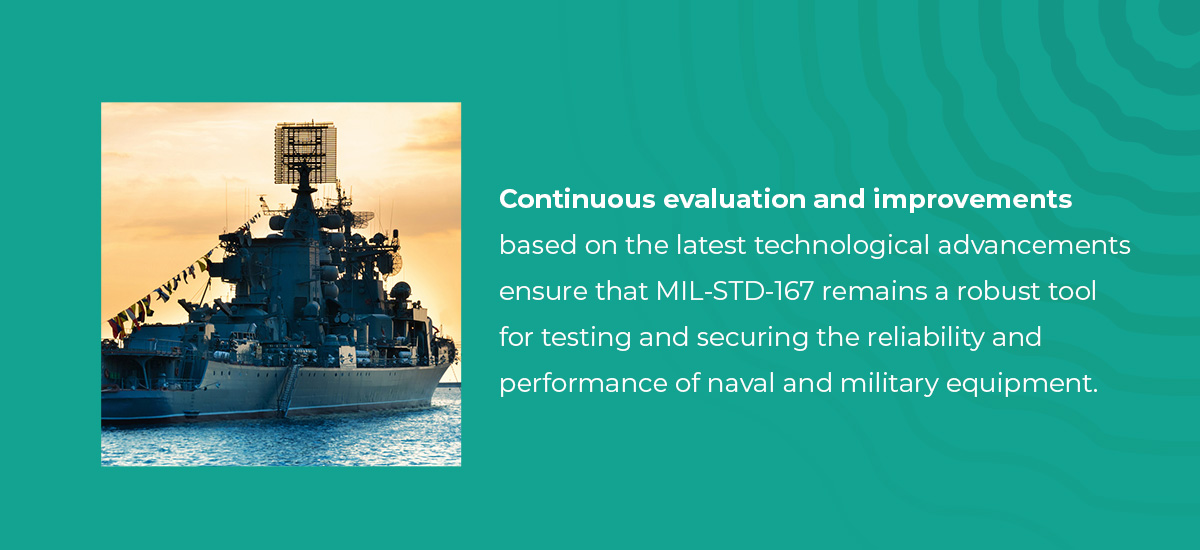
Continuous evaluation and improvements based on the latest technological advancements ensure that MIL-STD-167 remains a robust tool for testing and securing the reliability and performance of naval and military equipment.
Scope and Objectives
The standard outlines specific testing procedures, including vibration amplitudes, frequency range and the duration of testing. Its scope and objectives are designed to confirm the reliability of equipment intended for military use. Aside from wartime operations, where firing and other vessels can cause vibrations, this equipment is subjected to common vibrational conditions. To assess its performance and identify room for improvement, more common vibrations that are simulated include:
- Mounting system resonances
- An imbalance between propellers and shafting
- Propeller blade excitation
- Changes in the sea state
- A shift in ship heading and speed
It applies to a wide range of shipboard apparatus, including electrical, mechanical and electronic devices like communication devices, navigation systems and vessel control systems. Engine and propulsion systems like turbines operate at high speeds and, at times, need to perform evasive maneuvers, requiring them to withstand vibrations without failure. The weapon system and its components must also maintain operational readiness and accuracy under vibrational stress from firing and ship movement.Â
MIL-STD-167 Vibration Testing Methods
MIL-STD-167 covers two primary types of vibration test procedures — environmental and mechanical. Equipment manufacturers must demonstrate their compliance with MIL-STD-167 through these tests and their resulting certification. These methods do not test for system components or rugged computers, which is where MIL-STD-167-1 comes in. MIL-STD-167-1, or MIL-STD-167-1A as it is known now, tests the impact of mechanical vibrations on Navy shipboard equipment like workstations, their components and rugged servers.
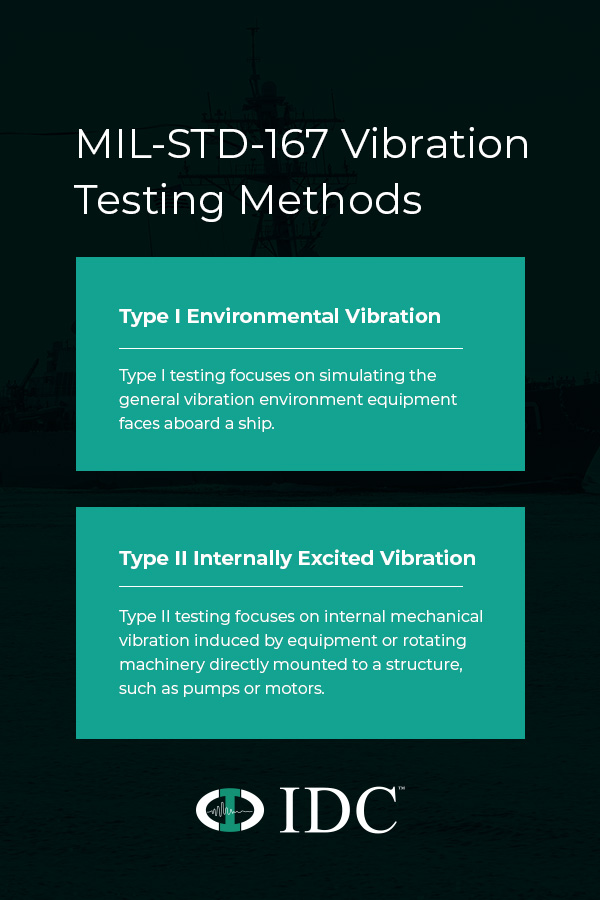
Type I Environmental Vibration
Type I testing focuses on simulating the general vibration environment equipment faces aboard a ship. It includes a vibration test, a frequency test, an endurance test and an endurance test from the vessel’s movement, sea conditions and other machinery. Each test, done separately, proves the equipment’s functional and physical integrity. During testing, equipment is in its operational state and secured to a shock and vibe table at the same points of attachment that are secured aboard a Navy vessel:
- Exploratory vibration test: The equipment is set on a table with a single amplitude of 0.010 ± 0.002 inches and vibrated at frequencies between 4 hertz and 33 hertz.
- Variable frequency test:Â At intervals of 1 hertz, equipment is vibrated at frequencies between 4 hertz and 33 hertz, per the table below. The frequency range depends on the blade rate frequencies associated with the design of the vessel where it is used.Â
- Endurance test:Â The endurance test for mounted equipment tests the frequencies at which equipment gets damaged, pushing the endurance from the previous two tests. Equipment vibrates for at least two hours at the desired frequency, building up to 33 hertz and 0.002-inch table amplitudes.
- Endurance test for mounted equipment:Â The MIL-STD-167-1 endurance test for mounted equipment vibrates for a minimum of two hours at 33 hertz unless the equipment meets predetermined exceptions.
Number of Endurance Test Frequencies | Test Time Duration at Each Frequency | Total Time |
---|---|---|
One | Two hours | Two hours |
Two | One hour | Two hours |
Three | 40 minutes | Two hours |
Four | 40 minutes | Two hours, 40 minutes |
n > 2 | 40 minutes | 40 × n minutes |
Type II Internally Excited Vibration
Type II testing focuses on internal mechanical vibration induced by equipment or rotating machinery directly mounted to a structure, such as pumps or motors. It helps stabilize rotor machinery to reduce internal vibration or excitation due to unstable rotating components with the following balancing methods:
Rotor Characteristics | Speed (RPM) | Type of Balancing | Balancing Limits and Methods |
---|---|---|---|
Rigid, L/D/ 1/<0.5* | 0 to 1000 | Single-plane | 5.2.2 |
 | > 1000 | Two-plane | 5.2.2 |
Rigid, L/D/ <0.5* | 0 to 150 | Single-plane | 5.2.2 |
 | > 150 | Two-plane | 5.2.2 |
Flexible | All | Multi-Plane | 5.2.3 |
*L represents the length of the rotor, exclusive of the shaft, and D represents the diameter of the rotor, using the same principle.
This category also specifies RPM, rotor characteristics and balancing types and procedures. The test equipment is mounted at a natural frequency that corresponds to a maximum of a quarter of the frequency associated with the unit’s minimal operational speed on the shipboard. During the test, engineers take note of the vibrational displacement and whether it exceeds the frequency range and amplitude.
Testing Procedures and Protocols
MIL-STD-167 testing procedures and protocols have detailed steps for preparing for, executing and documenting the results of vibration tests. Though the procedures are divided into Type I and Type II, the testing preparation, execution, and reporting processes are quite similar. A professional institution will conduct the official testing and issue the compliance certificate, but understanding the steps involved is still valuable to all stakeholders.
Preparation for Testing
Start by identifying the equipment that needs to be tested. This equipment represents production units in terms of construction, design and materials. Set up a controlled environment where shipboard conditions will be simulated. It may involve a vibration testing laboratory with the right equipment and space to conduct tests and deliver accurate results safely.Â
Select the vibration type by determining whether the equipment requires Type I or Type II testing. The type depends on the equipment’s installation and operational environment. Install the sensors and data acquisition systems on the equipment to measure the vibration response. Instrumentation must be calibrated and capable of recording vibration frequencies, amplitudes and durations accurately.
Mount the equipment securely on the vibration test platform to simulate its real shipboard installation. Ensure that the mounting method does not add extra stress or vibrations, which can interfere with results.
Executing Tests
Conduct a frequency sweep over a specified range to identify the resonant frequencies in the equipment’s maximum response. Perform a dwell test on identified resonant frequencies to test the equipment’s ability to withstand prolonged exposure to resonance. Apply vibrations at the specified levels to simulate environmental conditions or sinusoidal vibrations for internal testing. During the testing process, equipment response is monitored continuously, with parameter adjustments made to maintain compliance with the testing requirements.Â
All equipment must undergo functional tests before, during and after vibration testing to assess its operational performance and identify potential failure or degradation.
Documentation and Reporting
Test data is collected and analyzed to confirm that the equipment meets the vibration resistance requirements specified in MIL-STD-167. This allows time to identify any additional performance issues that occurred during testing. The data is then used to compile the report, which includes the following:
- Introduction:Â An introduction describing the test equipment and the purpose of the test.
- Test setup:Â Details of the testing instrumentation, environment and all mounting configurations.
- Testing procedures:Â An overview of the testing process, frequency sweeps, functional tests and resonance dwells.
- Results and analysis: A presentation of the test data from the vibration analysis for military equipment, including the equipment’s performance, compliance with standards and any identified resonances.
- Conclusion and recommendations:Â The conclusion of findings and recommendations for design modifications or retesting.
Comparison With Other Standards
Adhering to military standard testing (MIL-STD), detail specifications (MIL-DTL) and specifications (MIL-S) ensures that vehicles, vessels and the equipment they use perform as they should across various DoD operations. Standards similar to the MIL-STD-167 testing procedures include:
- MIL-STD 810:Â MIL-STD 810 focuses on testing procedures that determine how military equipment holds up under various conditions during usage, transportation and storage. These conditions include humidity, temperature and impact.
- MIL-S-901:Â The shipboard shock, or MIL-S-901 test, covers shock testing requirements for shipboard structures, equipment, machinery and other systems. It verifies their ability to withstand shock loadings that might occur during wartime service.
- MIL-DTL-901E: MIL-DTL-901E is a high-impact shock test for military vessels, similar to MIL-S-901, but this test includes submarines.Â
- MIL-STD-461:Â MIL-STD-461 EMI and EMC standards test the limits for electromagnetic interface characteristics (EMC) for electronic, electromechanical and electrical equipment emissions and susceptibility.
- MIL-STD-704: The MIL-STD-704 test for aircraft electric power establishes the characteristics and requirements for aircraft electric power. However, it excludes electromagnetic voltage and interference spikes.
- MIL-STD-1275:Â The test for military vehicle electrical systems. It tests the limits of steady state limits and transient voltage characteristics of the direct current (DC) and 28-volt electric power circuits on military vehicles.
Best Practices and Standards for MIL-STD-167 Compliance
Complying with MIL-STD-167 requires a structured approach. Best practices include understanding the requirements. Demonstrating proactivity by incorporating vibration-resistant features into equipment design, like vibration-dampening materials and shock absorbers, is also essential. Manufacturers must also use laboratories with experience in this testing method to ensure a proper test setup and accurate instrumentation.
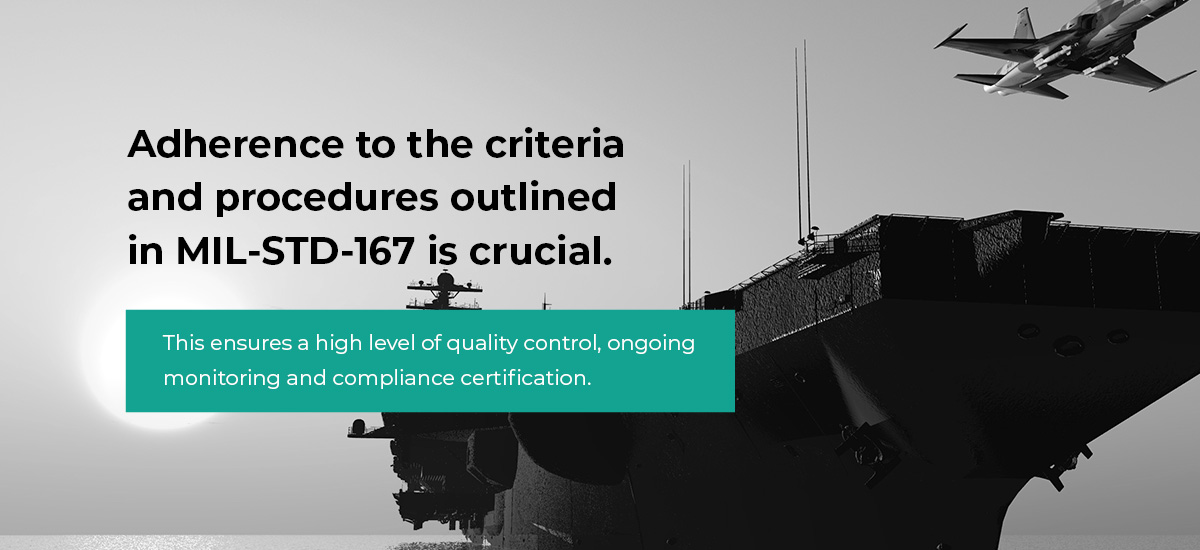
Adherence to the criteria and procedures outlined in MIL-STD-167 is crucial. This ensures a high level of quality control, ongoing monitoring and compliance certification. It verifies the equipment’s performance, enhancing its durability and effectiveness in challenging vibrational environments.
Frequently Asked Questions
Given the complex nature of MIL-STD-167, stakeholders like manufacturers, engineers and military personnel must thoroughly understand its implementation and requirements. These frequently asked questions will offer guidance and clarification on the essentials of ensuring military equipment can withstand the rigorous demands of its environment.
How Do You Comply With MIL-STD-167?
Complying with marine vibration testing standards involves an equipment assessment, design considerations that enhance vibration resistance, selecting a quality testing facility, and implementing the recommended improvements from the reporting. Following these steps will result in a certification that confirms compliance.
What Are Vibration Test Equipment?
Equipment used in vibration testing include:
- A vibration test system with electrodynamic and servo-hydraulic shakers.
- A vibration control system, including software and controllers.
- Mounting fixtures and custom fixtures to match specific equipment shapes.
- Accelerometers and displacement sensors.
- Data acquisition systems.
What Are Vibration Test Criteria?
The test criteria for MIL-STD-167 include Type I and Type II vibration tests with their respective frequency ranges, vibration amplitudes, resonance identification and dwell, and functional testing. If the equipment fails to demonstrate the ability to operate without significant performance degradation or failure under specified vibration conditions, it will meet the MIL-STD-167 test criteria.
Does MIL-STD-167 Include Naval Equipment Testing Standards?
Yes, the vibration test procedures for military equipment do include testing naval equipment to ensure it withstands the mechanical vibrations encountered on ships. It is approved by all DoD agencies, the Naval Sea Systems Command and the Department of the Navy.
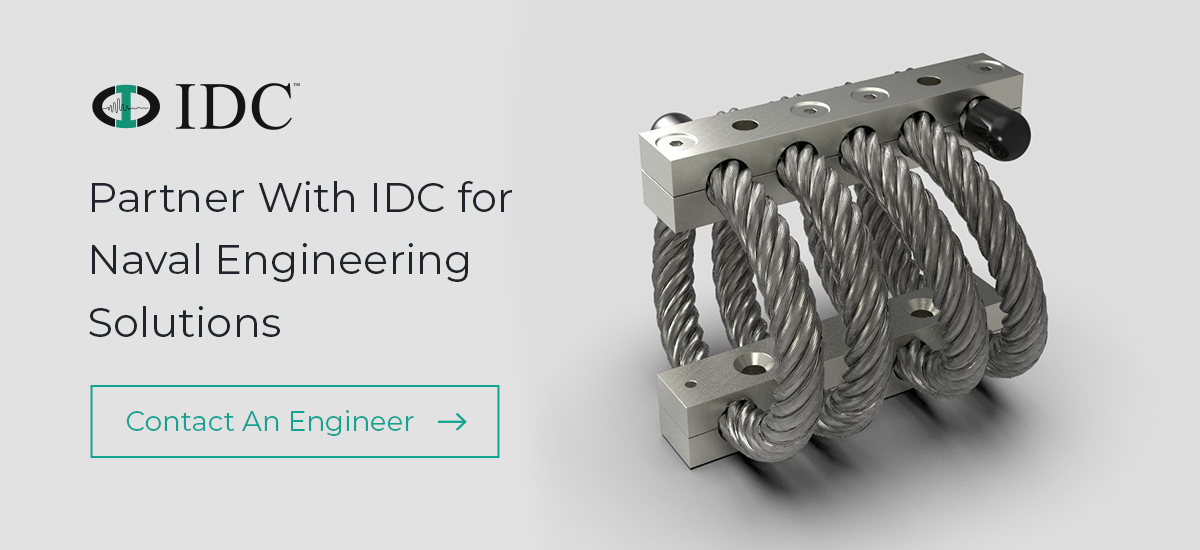
Partner With IDC for Naval Engineering Solutions
MIL-STD-167 applies to a wide range of shipboard equipment, including mechanical systems, electronic devices and electrical components. It ensures that all equipment can operate effectively in a naval ship’s challenging vibration environment. Compliance with MIL standards allows the military and manufacturers supplying them to better prepare for modern naval operations’ demands.
The knowledgeable professionals at IDC are experts at shock and vibration applications, including military vibration testing standards like MIL-STD-167. Our isolators add stability and strength to mission-critical rope and cable systems. We have a proved track record of providing reliable solutions to the United States Navy, Marines and Air Force.
Contact IDC today for unique engineering solutions for your military and defense systems.
Speak with a Sales Representative
Our representatives have a wealth of knowledge on all our products – let them steer you in the right direction.
Learn More